In October 2022 Danlers Ltd, a family-owned, UK specialist in energy saving, lighting controls contacted us because they were looking for a new manufacturing partner.
It promised to be a large project involving the transfer of 90 injection mould tools, followed by the set-up, trialling & validation of 106 lighting components and assemblies.
Our teams met, talked, looked at drawings, discussed process and after many discussions, agreed the partnership could work.
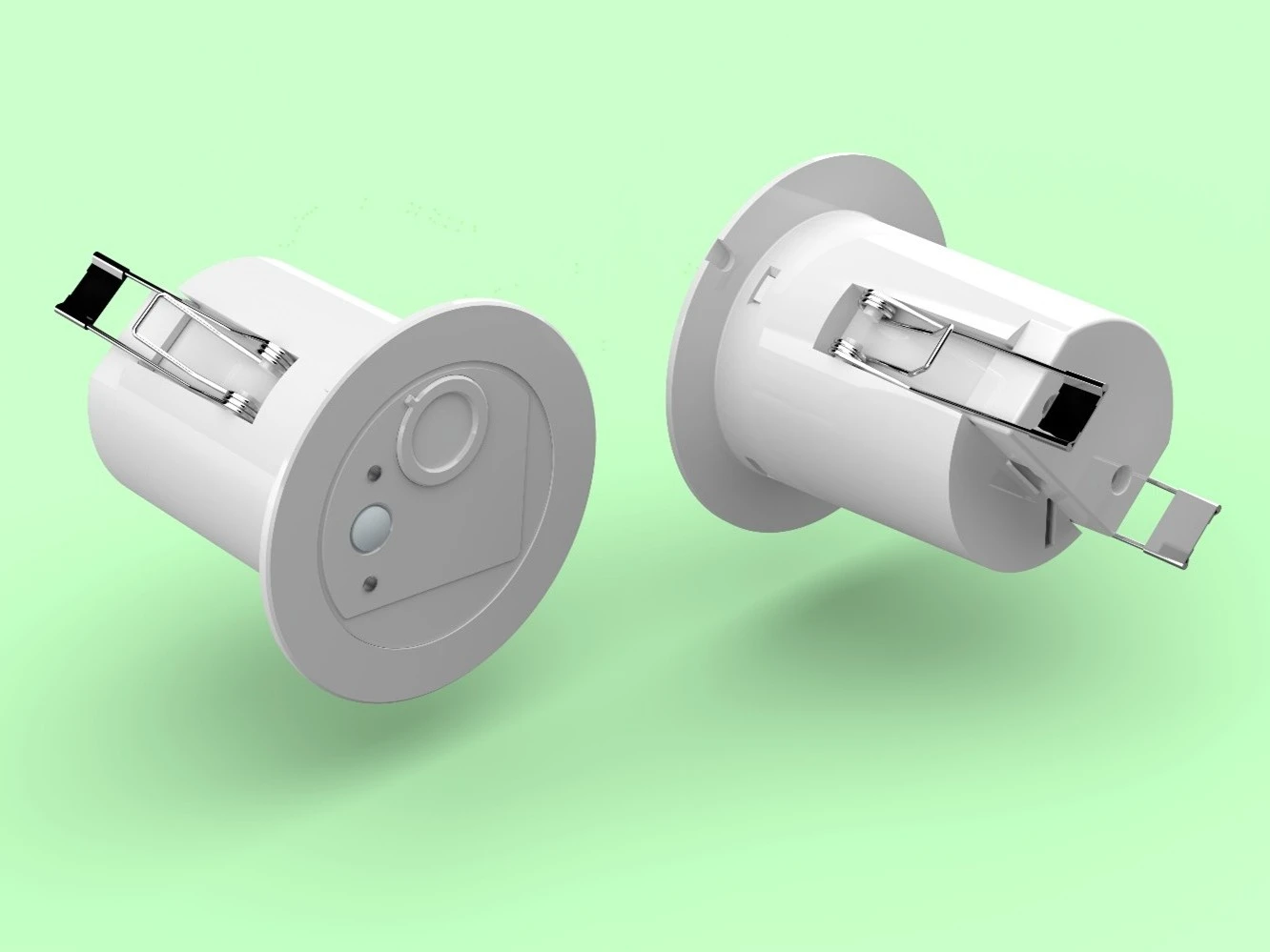
So, in April 2024, we began.
The Danlers Transfer Project
There is an established process for this type of transfer. The 90 injection mould tools arrived at our warehouse on pallets, where each one was catalogued and assessed by our team.
One by one, they were transferred to our in-house tool shop, IMT, where they were serviced or repaired.
Meanwhile, the data for the new parts was processed in our New Projects office, so each had the documentation in place before tool trials and validation began.
The processing team was led by Steve Wretham, our Senior Process Engineer, who was responsible for the initial mould trials for each part.
Once we had good parts in hand, New Projects and the Quality Department established controls, with dimensional reports (ISIRs) carried out, PPAP and production documents prepared and once all this is in place the parts are ready to be signed off for production.
It is a complicated and labour-intensive process to ensure that the parts that leave our facility, are the best condition they can be robust, repeatable and delivered on time.
Now, a year later, with all parts in production, we can reflect on the outcome and agree that the process went incredibly well, with the primary reasons for this success being:
- The components were well-designed
- The engineering and purchasing team from Danlers supported the process throughout.
- The WHP New Projects team co-ordinated the process with great efficiency.
- Our company values mutually align, making working together a pleasure and not a chore.
We consider the leap of faith that Danlers made, a significant compliment and very pleased that we delivered the project in such an efficient way that met (and hopefully exceeded) their expectations
We recently received this letter from their CEO, Kevin Johnstone.
“I’m writing to express our sincere gratitude for the outstanding service and quality products you have provided over the past year.
Your dedication to delivering high-quality materials and exceptional customer service has been a key part of our ability to deliver quality products and service to our customers in these trying times.
We greatly appreciate the attention to detail, reliability, and professionalism that your team consistently demonstrates.
We look forward to continuing our strong partnership in the year ahead and are confident that White Horse Plastics will remain a valued supplier to us.
Thank you all once again for your hard work and commitment.”
During this process we were awarded a brand-new project for Danlers involving 9 new mould tools, which is now ready to go into volume production and look forward to further developing our working relationship in the years to come.
For more information about Danlers and their latest range of Smart PIR sensors, please visit their website. If you are currently exploring options or are interested in finding out more about transferring your injection moulding requirements to White Horse Plastics, we look forward to hearing from you. You can submit your enquiry via our contact page.